For optimal production processes
Various PVD coatings are used in punching and forming applications on tool components. While a hard coating is required to protect the cutting edge during the cutting process, various PVD coatings are applied for complex forming processes.
Areas of application
Cutting
Cutting blades and brake tools are coated for wear protection
Punching
PVD coating of stamps and dies to increase tool life in punching processes
Forming
Possible PVD applications are bending, deep drawing and embossing tools
Massive forming
Massive forming, hot forming and forging are marginal PVD applications
PVD coatings for punching and forming
DLC 4000
Tool coating for punching and forming of aluminum
CrN
PVD coating for processing copper and non-ferrous alloys
TiCN
Universal coating of stamping and forming tools for steel materials
DUPLEX VARIANTIC
PVD coating for the more massive forming processes of thicker steel sheets
Advantages of PVD coatings for punching and forming
Wear protection coating for increased tool life of stamping and forming tools
Improved surface and cut surface quality by use of coating
Reduction of friction, adhesion and material build-up during application
Reduction of lubricant use to the extent of dry forming processes
Increase of stroke rates during stamping and reduction of drawing steps during forming
Improvement of shaping, dimensional accuracy and surface quality
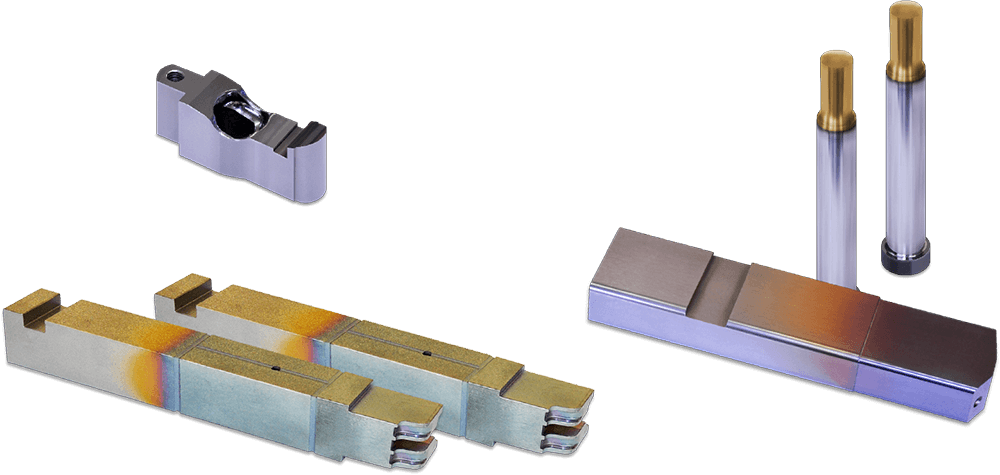